Predictive maintenance adalah suatu metode perawatan yang didasarkan pada data untuk kemudian dianalisis agar bisa mendeteksi adanya anomali pada sebuah alat atau sistem. Berbeda dengan tipe maintenance yang lain, perawatan ini memanfaatkan cukup banyak perlengkapan canggih seperti Artificial Intelligent (AI).
Bila dilakukan dengan benar, perawatan prediktif bisa memberikan keuntungan tersendiri. Misalnya mengurangi membengkaknya budget akibat kerusakan mendadak.
Seperti apa langkah-langkah perawatan ini? Apa saja keuntungannya? Agar lebih jelas, mari pahami dulu pengertiannya menurut para ahli.
Apa itu Predictive Maintenance?
Berikut beberapa pengertian predictive maintenance menurut para ahli:
- CCPS (Center for Chemical Process Safety). Predictive maintenance artinya maintenance yang didasarkan pada data dari kondisi real-time dan apakah data tersebut sejalan dengan performa normal suatu mesin.
- Bentley. Perawatan prediktif adalah upaya maintenance yang meliputi kegiatan monitoring pada beberapa kondisi atau variabel yang terkait dengan peralatan.
- Calixto. Predictive maintenance merupakan hal yang penting dilakukan untuk mengidentifikasi potensi kerusakan dan menjelaskan kapan dilakukannya tindak preventif sebelum kerusakan fungsional terjadi.
- Mokhatab, Poe, dan Mak. Pengertian predictive maintenance ialah metode untuk memprediksi masa pakai komponen penting berdasarkan inspeksi atau diagnosis untuk memaksimalkan penggunaan komponen tersebut.
- Sinha, Dixit, Chakrabarty, dan Jain. Definisi pemeliharaan prediktif merupakan perawatan berdasarkan kondisi yang ditemukan untuk mengevaluasi peralatan berdasarkan monitoring periodik ataupun kontinyu.
Berdasarkan beberapa pengertian di atas, bisa disimpulkan bahwa predictive maintenance adalah tipe maintenance yang dilakukan berdasarkan data untuk mengevaluasi peralatan sehingga dapat dilakukan perbaikan sebelum kerusakan terjadi.
Tujuan Predictive Maintenance
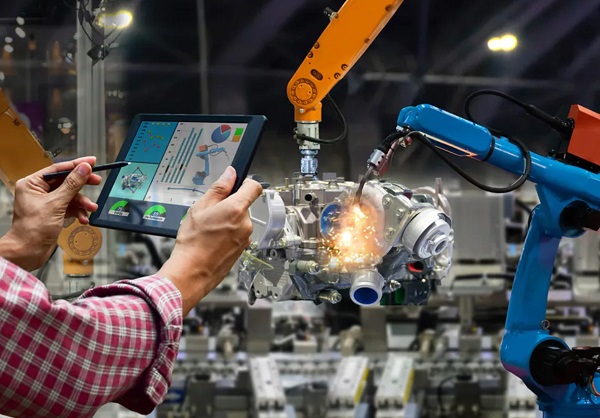
Adapun tujuan pemeliharaan prediktif ialah:
1. Meningkatkan Efisiensi Maintenance
Perawatan prediktif secara umum lebih efisien dibanding perawatan yang lain. Dus, salah satu tujuan umum dilakukannya maintenance ini adalah untuk efisiensi dalam hal perawatan aset.
2. Menurunkan Budget
Tak jarang, maintenance dilakukan saat alat sudah rusak atau ketika sistem justru dalam kondisi yang masih baik. Hal-hal seperti ini pada akhirnya hanya membuang-buang budget. Perawatan prediktif bertujuan untuk mereduksi pemborosan tersebut dengan sistem yang lebih akurat.
3. Memaksimalkan Produktivitas
Dengan kemampuannya mendeteksi eror, perbaikan bisa dilakukan sebelum terjadi kerusakan total. Alur produksi pun akan senantiasa lancar sebab alat tidak mengalami kerusakan mendadak.
Peralatan Predictive Maintenance
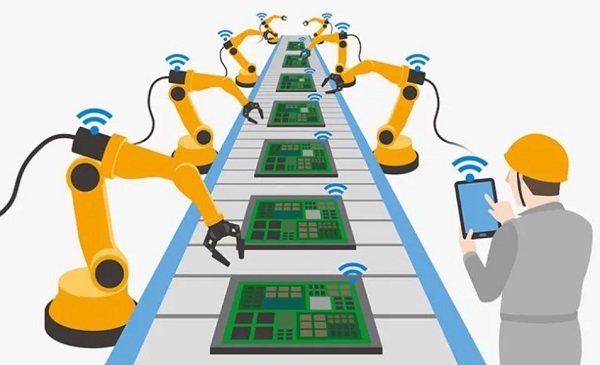
Terdapat cukup banyak peralatan yang bisa digunakan dalam proses perawatan prediktif. Namun yang utama adalah:
1. Alat Pengambilan Data
Alat pengambilan data adalah semua alat yang bisa digunakan untuk memperoleh data sensorik seperti getaran, suhu, noise, hingga tekanan. Jenis alatnya tentu beragam. Misalnya vibration meter untuk mendapatkan data getaran hingga kamera infrared untuk mendeteksi titik panas suatu sistem.
2. IoT
IoT atau Internet of Things berguna untuk mengubah informasi dari alat pengambil data (misalnya suhu atau getaran) ke dalam suatu sinyal digital. Pengubahan ini dilakukan supaya data lebih mudah dianalisis lebih lanjut.
3. Machine Learning
Machine learning akan mengumpulkan semua sinyal digital dan mengolahnya untuk memetakan karakteristik yang normal pada sebuah alat atau mekanisme. Misal, suatu alat bisa disebut normal bila tidak melewati suhu tertentu. Ketika suatu hari terdeteksi suhu yang terlalu tinggi, artinya terjadi anomali yang perlu pemeriksaan lanjutan.
4. CMMS
Computerized maintenance management system atau CMMS akan menghasilkan semacam perintah kerja bagi teknisi maintenance. Perintah tersebut didasarkan pada deteksi anomali dari pola normal suatu alat.
Prosedur Predictive Maintenance
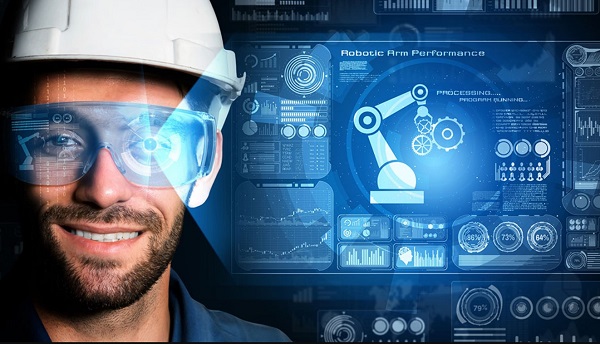
Berikut langkah langkah saat hendak melakukan predictive maintenance:
1. Analisis Data Awal
Pada tahap ini, semua data awal seperti laporan maintenance yang pernah dilakukan hingga CMMS dikumpulkan. Setelah itu data dianalisis sebagai pertimbangan untuk menentukan langkah selanjutnya.
2. Identifikasi Kerusakan dengan Mode Failure
Identifikasi kerusakan pada mode failure dilakukan untuk mendapatkan data mengenai frekuensi terjadinya kerusakan, tingkat keparahan kerusakan yang terjadi, hingga kesulitan saat melakukan deteksi kerusakan. Data ini pun nantinya dipakai untuk mempertimbangkan langkah berikutnya.
3. Pengumpulan Data Sensorik
Pengambilan data wajib dilakukan secara langsung. Pemilihan komponen yang hendak diambil datanya sendiri sebaiknya didasarkan pada hasil analisis pada langkah 1 dan 2.
Misalnya, berdasarkan laporan yang terdahulu, ditemukan bahwa pipa A pernah mengalami kebocoran. Dus, bagian inilah yang semestinya diperiksa lebih lanjut.
4. Analisis Data
Langkah berikutnya adalah melakukan analisis atas semua data yang diperoleh. Analisis bisa dilakukan dengan bantuan AI dan machine learning untuk menentukan pola normal dan anomali suatu alat.
5. Penetapan Warning untuk Teknisi
Berdasarkan hasil analisis, sebuah alarm atau peringatan bisa dibuat agar teknisi melakukan inspeksi ketika terdeteksi anomali. Caranya dengan menghubungkan peralatan monitoring dengan CMMS yang bisa mengeluarkan perintah kerja.
Beda Predictive Maintenance Dengan Maintenance Lainnya
Tipe maintenance yang dapat dilakukan sebenarnya cukup beragam. Reactive maintenance, misalnya, merupakan perawatan yang dilakukan pada alat yang terlanjur rusak.
Selain itu, terdapat pula preventive maintenance. Sekilas, tipe perawatan ini hampir sama dengan perawatan prediktif. Akan tetapi, preventive maintenance tidak dilakukan berdasarkan data. Preventive maintenance didasarkan pada waktu, misalnya maintenance mingguan, bulanan, dan tahunan.
Keuntungan Predictive Maintenance
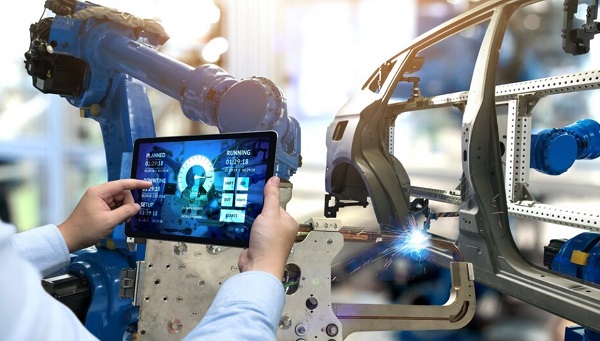
Keunggulan pemeliharaan prediktif ialah:
1. Meminimalisir Frekuensi Maintenance Tak Terencana
Perawatan prediktif dapat meminimalisir reactive maintenance. Hal ini dikarenakan dilakukannya monitoring data secara real time sehingga kerusakan produk bisa dicegah.
2. Menurunkan Biaya Preventive Maintenance
Preventive maintenance kadang memakan biaya sangat besar sekiranya alat dalam kondisi baik-baik saja atau malah terlanjur rusak parah. Aplikasi perawatan prediktif yang berbasis real time data jelas bisa meminimalisir hal-hal seperti itu dan dengan demikian bisa mencegah pemborosan.
3. Predictive Maintenance Mampu Meningkatkan Masa Pakai Alat
Deteksi eror sejak dini yang dilakukan pada proses perawatan prediktif dapat meningkatkan kondisi alat. Usia alat pun bisa bertambah mulai dari 20% hingga 40% dari masa pakai normalnya.
4. Mengurangi Budget Pekerja dan Pembelian Suku Cadang
Labour cost dan pembelian suku cadang bisa mengalami pembengkakan apabila sistem tidak bekerja dengan baik. Perawatan prediktif dapat mengatasi kedua hal tersebut dengan efektivitas monitoringnya.
5. Predictive Maintenance Mencegah Kerusakan Komponen
Anomali data belum tentu menunjukkan bahwa komponen tersebut telah rusak. Kadangkala, komponen hanya perlu dibersihkan, diberikan pelumas, dan hal-hal sejenis lainnya. Dus, dengan diterapkannya perawatan prediktif, eror yang ditemukan bisa segera diatasi sehingga kerusakan yang lebih parah bisa dicegah.
6. Melindungi Pekerja
Kondisi kerja terutama yang berkaitan dengan alat elektronik selalu memiliki resiko tersendiri. Upaya untuk meningkatkan keamanan bisa dilakukan dengan memastikan bahwa sistem dan komponennya berada dalam kondisi baik. Dus, perawatan prediktif yang bisa digunakan untuk mengetahui hal tersebut pun bisa meningkatkan keselamatan bagi para karyawan.
Kekurangan Predictive Maintenance
Selain kelebihan, juga terdapat beberapa hambatan predictive maintenance, yaitu:
1. Perencanaan yang Lebih Rumit
Meski efektif mencegah kerusakan, namun maintenance ini membutuhkan perencanaan yang rumit. Detail-detail harus diperhatikan yang memakan waktu lama.
2. Budget Bertambah untuk Pembelian Alat Maintenance
Alat yang diperlukan untuk perawatan prediktif tidaklah murah. Beberapa peralatan harus dibeli dengan harga yang tinggi.
3. Sangat Tergantung pada Peralatan
Tipe maintenance ini sangat tergantung pada alat, baik untuk pengambilan data ataupun analisisnya. Meski metode tersebut terbilang modern, namun kadangkala eror analisis juga bisa terjadi.
4. Tak Bisa Dilakukan Sembarang Orang
Selain harga alatnya mahal, tak semua pekerja bisa mengoperasikannya. Tak jarang, sebuah perusahaan harus menyewa pihak ketiga untuk melakukan predictive maintenance. Dengan kata lain, budget yang harus disediakan pun harus ditambah lagi.